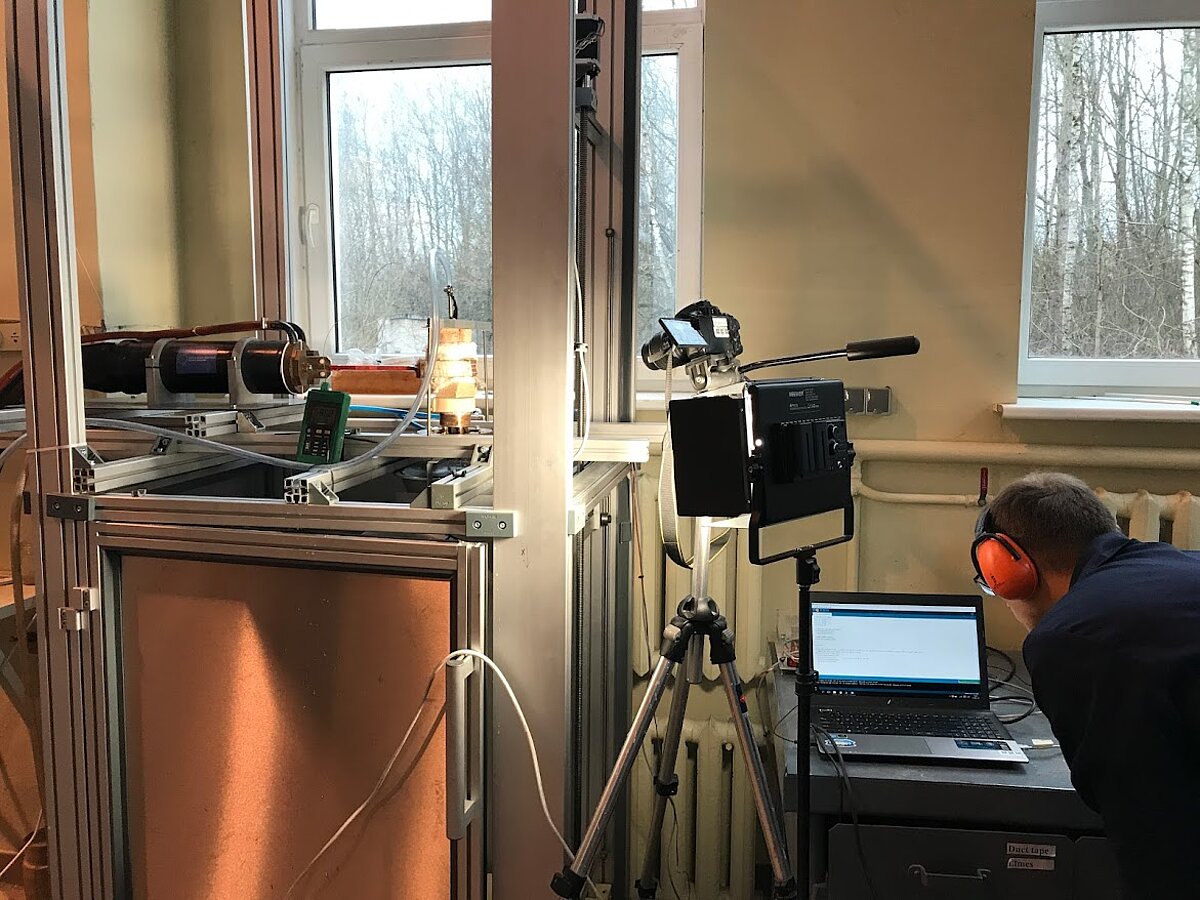
In the automotive, aviation and space industries, reducing the weight of components is essential, as it is directly related to the consumption of fuel or energy. Metal 3D printing and high-performance materials are considered to be amongst the most promising ways to weight reduction.
“Metal 3D printing is significantly more complex than conventional metalworking, yet it is potentially economically feasible also with more expensive high-performance alloys, as the process has minimal loss of material,” emphasize the researchers.
Aluminium matrix composites (AMC) are among the most promising classes of such materials. AMC are aluminium alloys that consist of the alloy itself and micro- and nano-sized ceramic particles mixed into it, thus providing the final material with better mechanical, thermal, and other properties.
AMC is basically produced by powder metallurgy. This method requires raw materials that are 5–10 times more expensive than those necessary in case of the production processes in metallurgy. At the same time, it is impossible to produce AMC wire with classical metallurgical methods and a range of tools designed for working with liquid metal. Electromagnetic effects constitute unique tools that open up new possibilities for material processing. Furthermore, these effects include non-contact methods with the respective advantages.
Researchers of the MHD Technology Laboratory of the UL Institute of Physics have conducted research to develop a new technological process for the metallurgical production of AMC, using electromagnetic methods. The developed process consists of three consecutive steps that allow the AMC material to be obtained metallurgically by using electromagnetic methods.
- The first step in the production of AMC – the particles are mixed into liquid aluminium alloy using a permanent magnet stirrer. It has been shown theoretically and experimentally that a rotating permanent magnet can produce an intense flow of liquid metal, which mixes particles into the alloy from its surface.
- The particles mixed in the alloy have a tendency to “stick together” or form agglomerates. Therefore, the second step in the production of AMC constitutes dispersion of the particles in the alloy. Researchers have shown that with combined impulse and constant magnetic field treatment, a significant improvement in particle distribution in the alloy can be achieved, making it homogeneous and free of agglomerates.
- In order to use the alloy for 3D printing applications, it is necessary to obtain material for AMC wire. For this purpose, a continuous casting crystallizer, or equipment, has been developed, which allows controlled production of an aluminium rod with homogeneous properties, thus enabling the AMC production process to be made continuous in the future.
The AMC bar is then treated mechanically and thermically, transforming it into a wire.
The main result of the project is the developed technological process, which is scalable and prospective for development to an industrial production process. As a result of the project, technology readiness level (TRL) 5 was achieved, demonstrating all 3 aforementioned production steps in a single technological prototype. In addition, the resulting wire was used to print small-scale parts to demonstrate the use of the technology in the automotive, aviation and space industries.
SIA “2AM” is a dynamically growing company engaged in the development and production of high-performance lightweight Al-Mg-Sc alloys and metal matrix nanocomposites. The team of SIA “2AM” includes business professionals and experienced doctoral level researchers specializing in advanced materials and technologies, engaged in research, development and production of advanced materials for the aviation and space industries.
The project was financed from the funds of the European Regional Development Fund (ERDF), Project ID No. 1.1.1.1/19/A/080 “Electromagnetic processing during solidification of nano-particle strengthened light alloys for additive manufacturing”. Total project duration: 36 months.
menang123, togelup, menang123, menang123, menang123, menang123, eurotogel, olx88, lapakgaming, hebat99, maret88, menang123
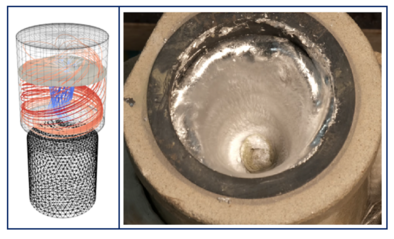
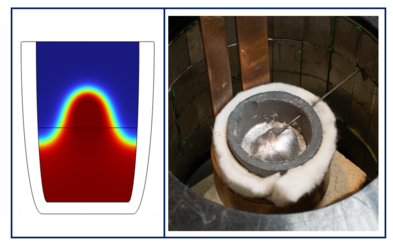